The most basic fluid conveyance machinery used in industrial production is the pump. Due to their different structural characteristics and operating principles, centrifugal and reciprocating pumps—the two primary types of pumps—have very different performance and application scenarios. The two types of pumps will be thoroughly compared in this article from a number of angles, such as application scopes, performance traits, and operating principles.
Differences in Working Principles
The centrifugal force is the foundation of working principle of a centrifugal pump. When the motor drives the impeller to rotate at a high speed, the fluid is thrown from the center of the impeller to the outer edge. During this process, kinetic energy is converted into pressure energy. The fluid is collected by the volute and then discharged from the outlet. This working principle determines that the centrifugal pump has the characteristics of uniform flow rate and stable operation.
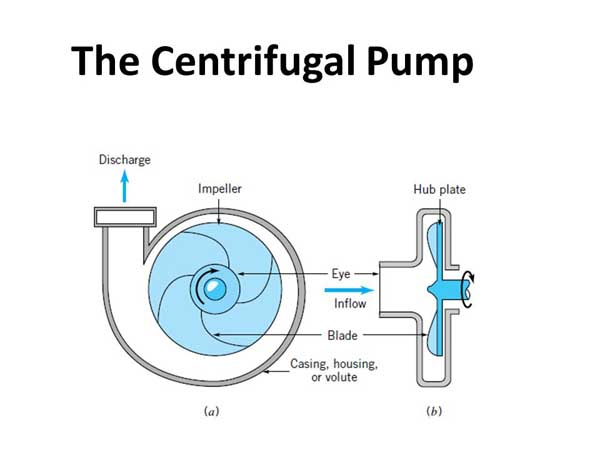
Conversely, the volumetric working principle is used by reciprocating pumps. The fluid is drawn in and released by the reciprocating action of the cylinder’s piston or plunger and the alternating opening and closing of the inlet and outlet valves. Although the pump may generate a high discharge pressure in this working mode, flow pulsation becomes an issue.
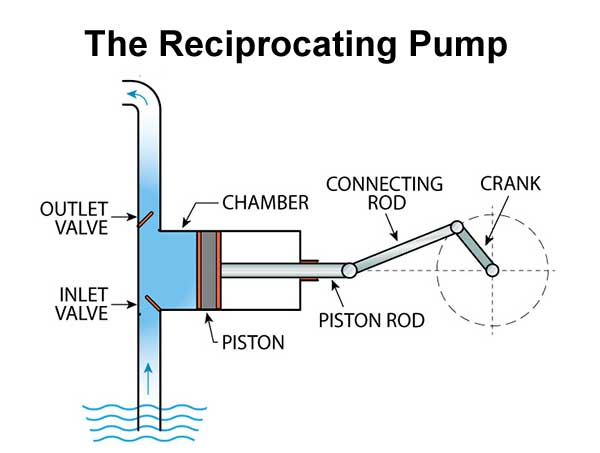
Comparison of Performance
Flow Characteristics
Centrifugal pumps offer a large, continuous, and stable flow, making them suitable for applications requiring a constant flow rate. In contrast, a buffer device is typically required to lessen the periodic pulsation in the flow of reciprocating pumps.
Pressure Capacity
Because they can generate pressures of up to 100 MPa, reciprocating pumps are especially well-suited for high-pressure applications. In contrast, centrifugal pumps have a relatively small pressure capacity, typically no more than 5 MPa.
Efficiency Performance
Centrifugal pumps normally have a limited high-efficiency zone and an efficiency range of 60% to 80% at rated conditions. The efficiency of reciprocating pumps can reach 70% to 90% and remain relatively high under a variety of operating conditions.
Medium Adaptability
Centrifugal pumps are suitable for conveying clean, low-viscosity liquids. The efficiency drops significantly when the viscosity of the medium exceeds 500 cSt,. Reciprocating pumps, however, are more adaptable to high-viscosity media such as crude oil and asphalt.
Comparison of Structural Characteristics
Centrifugal pumps are easy to maintain and have a relatively simple structure made up of parts, including the shaft seal, pump casing, and impeller.
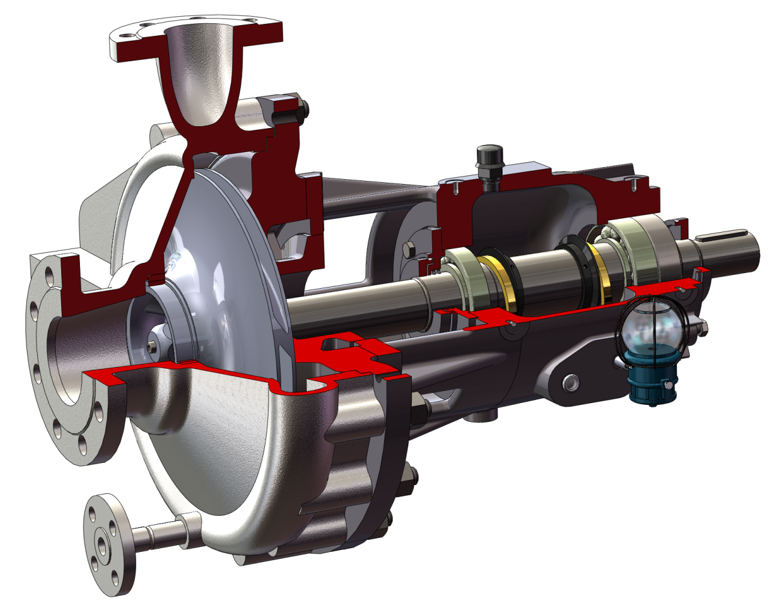
Reciprocating pumps have a more complex structure, including multiple precision components such as pistons, cylinder liners, and valves, and require a higher level of maintenance.
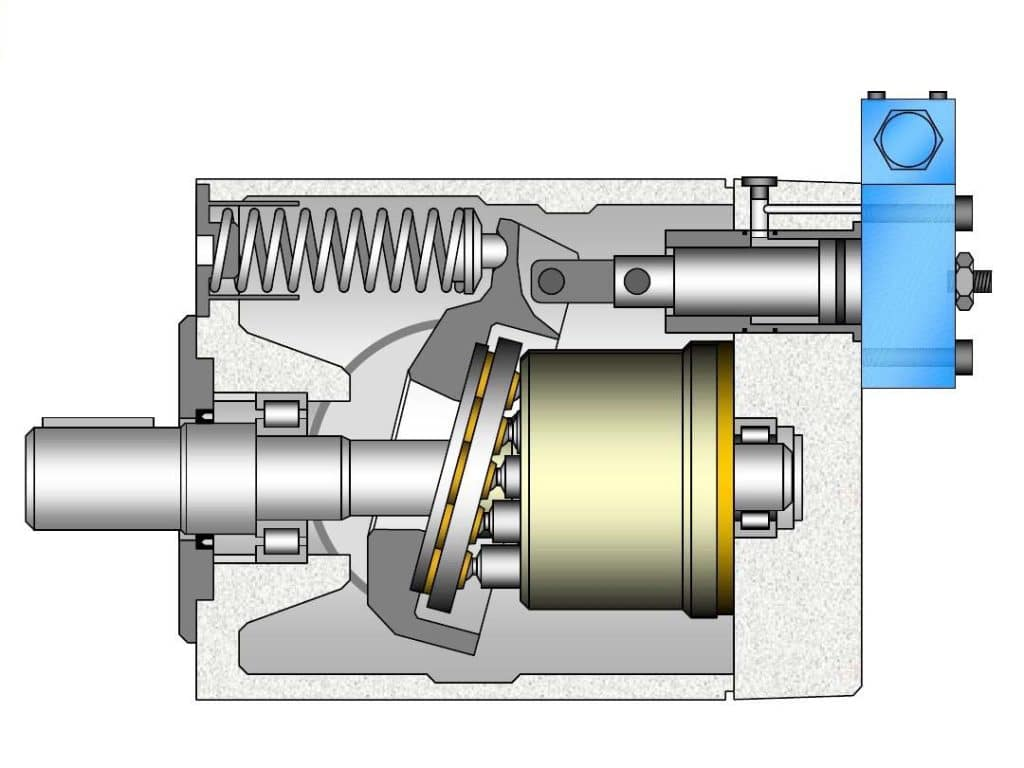
For the same flow rate, centrifugal pumps are often lighter and more compact in size. Reciprocating pumps tend to be larger in volume as they need to balance inertial forces.
Application Scenario Selection
Typical applications of centrifugal pumps include:
- Municipal water supply systems
- Liquid conveyance in chemical processes
- Air-conditioning circulation systems
- Large-flow irrigation
Centrifugal Pump
Reciprocating pumps are more suitable for the following scenarios:
- High-pressure water injection in oil extraction
- Quantitative dosing in chemical production
- Conveyance of viscous materials in the food industry
- Applications requiring precise measurement
Selection Recommendations
When selecting a pump in practice, the following factors should be considered:
- Determine the characteristics of the medium (viscosity, corrosiveness, solid content, etc.).
- Define the operating conditions (pressure and flow rate ranges).
- Evaluate the operating costs (energy consumption and maintenance expenses).
- Consider the installation space limitations.
Generally, for the conveyance of clean media with large flow rates and medium-to-low pressures, centrifugal pumps are the preferred choice. For high-pressure, high-viscosity applications or those requiring precise measurement, reciprocating pumps are more suitable.
Development Trends
As technology develops, the two kinds of pumps are becoming more similar. The rotational speed of new high-speed reciprocating pumps is continuously increasing, and intelligent centrifugal pumps are equipped with better adjustment performance. The use of digital monitoring technology has improved the efficiency and convenience of managing and maintaining both kinds of pumps.
In conclusion, there is no definitive superiority or inferiority between centrifugal and reciprocating pumps; each has advantages of its own. For maximum energy efficiency and financial gains, engineering specialists should choose the best pump type based on particular operating conditions.